Alüminyum Ekstrüzyonu Anlamak
Alüminyum ekstrüzyon, alüminyum hammaddesinin veya alüminyum alaşımlı malzemenin belirli bir kesit profiline sahip bir kalıptan geçirilerek preslenmesini içeren bir prosedürdür.
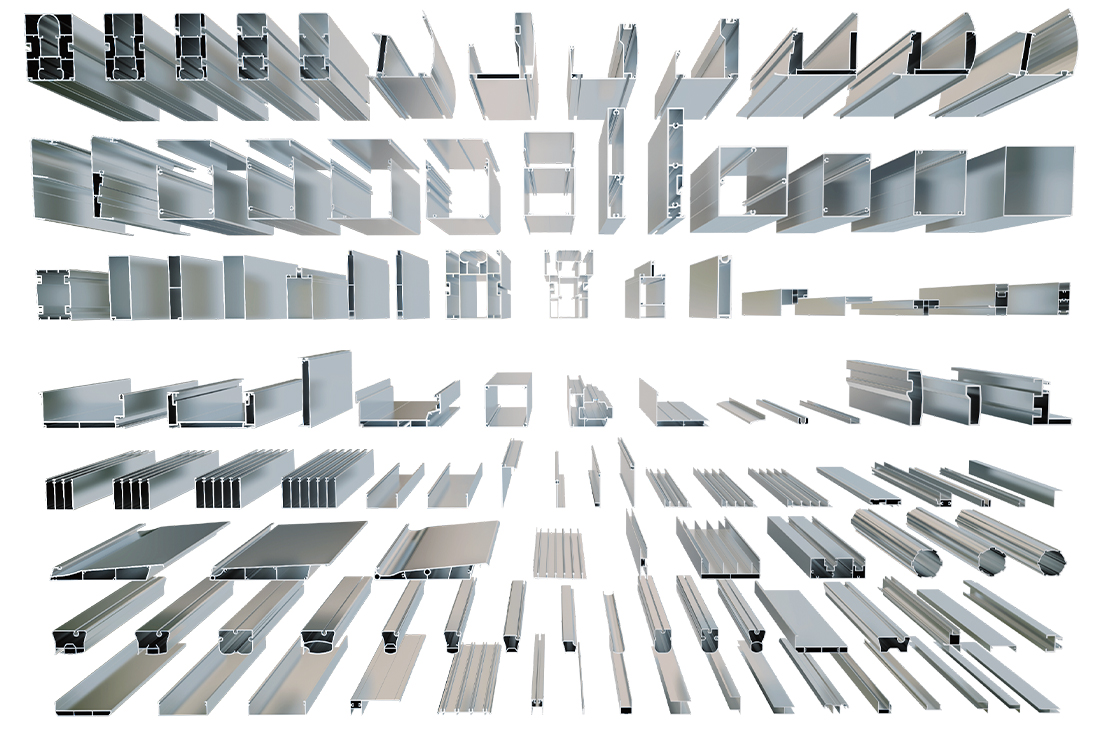
Alüminyum ekstrüzyon, alüminyum hammadde veya alüminyum alaşımlı malzemenin belirli bir kesit profiline sahip bir kalıptan preslenmesini içeren bir prosedürdür. Alüminyumun geniş bir kullanım yelpazesine uygun nesnelere dönüştürülmesi için kullanılır. Alüminyumun işlenebilirliği, şekillendirilmesini ve dökülmesini kolaylaştırır ve çeliğin üçte biri yoğunluğa ve sertliğe sahip olduğundan, ortaya çıkan ürünler diğer metallere kıyasla güçlü ve sağlamdır.
Son zamanlarda alüminyum ekstrüzyon, ürün geliştirme ve üretim alanında baskın bir güç haline gelmiştir. Son araştırmalara göre, küresel alüminyum ekstrüzyon pazarı 2022'de 86,16 milyar dolardan, 2023'te %7,7'lik yıllık bileşik büyüme oranıyla (CAGR) 92,8 milyar dolara yükseldi.
Belki de bu üretim yöntemiyle karşılaşmış ve inceliklerini merak etmişsinizdir. Bu makale, alüminyum ekstrüzyonun doğası ve mekaniği hakkında içgörüler sunarak kapsamlı yönlerini araştırıyor.
Alüminyum Ekstrüzyonu Neleri İçerir?
Alüminyum ekstrüzyonu, bir alüminyum alaşımının özel olarak tasarlanmış bir kalıptan geçirilerek farklı bir kesit şekli elde edilmesini içerir. Alüminyumu kalıptan geçirmek için önemli bir kuvvet uygulanır ve alüminyum kalıbın tasarımının tam şeklini alır. Bu gerçekleşirken, ekstrüde alüminyum bir konveyör üzerinde taşınır.
Kavramı basitleştirmek için: bir tüp diş macununu sıktığınızı hayal edin. Siz basınç uyguladıkça, macun tüpün memesi tarafından şekillendirilerek çıkar. Benzer şekilde, diş macunu tüpünün memesi de bu süreçte ekstrüzyon kalıbına benzer bir amaca hizmet eder.
Alüminyum Ekstrüzyonun Arkasındaki Tarihçe
Bu üretim yönteminin kökenleri bir asır öncesine dayanmaktadır. Joseph Bramah ilk olarak 1797'de kurşun boru üretimi için ekstrüzyon işlemini tanıtmıştır. Başlangıçta "fışkırtma" olarak adlandırılan bu yöntem, Thomas Burr'un ilk hidrolik pres ile yenilik yaptığı 1820 yılına kadar manuel olarak kaldı. Daha sonra, 1894 yılında Alexander Dick, bugün hala yaygın olan bir yöntem olan sıcak ekstrüzyon tekniğini tanıttı. Bu ilerleme, ekstrüzyonda demir dışı alaşımların kullanılmasını sağladı. 1904 yılına gelindiğinde, ilk alüminyum ekstrüzyon presinin icadının ardından, otomotiv ve inşaat sektörlerinde alüminyum uygulamalarında önemli bir artış görüldü.
Küresel savaşlar, özellikle uçak imalatında olmak üzere askeri uygulamalar için gerekli hale geldiğinden alüminyum ekstrüzyona olan talebi daha da hızlandırdı. O zamandan bu yana ekstrüzyon alüminyumun kullanımı artmış ve verimli üretim metodolojisine bağlı olarak kullandığımız araçlardan sıradan ev eşyalarına kadar günlük hayatımızın çeşitli yönlerine nüfuz etmiştir.
Doğrudan ve Dolaylı Alüminyum Ekstrüzyon Tekniklerini Anlama
Alüminyum ekstrüzyonu temel olarak iki farklı süreç izler: doğrudan ve dolaylı. Doğrudan ekstrüzyonda kalıp sabit kalır ve koç metali içinden itmek için kuvvet uygular. Öte yandan, dolaylı teknikte kütük sabit kalırken kalıp ona karşı hareket eder ve metali itmek için gerekli basıncı oluşturur. Şimdi bu iki yaklaşımı daha derinlemesine inceleyelim.
Doğrudan Alüminyum Ekstrüzyon Tekniği
İleri ekstrüzyon olarak da bilinen doğrudan ekstrüzyon, alüminyum ekstrüzyonuna yönelik en yaygın yaklaşımdır. Bu yöntemde, makinistler esasen ısıtılmış alüminyum olan kütüğü ısıtılmış duvarları olan bir kabın içine yerleştirir. Daha sonra bir şahmerdan kuvvet uygulayarak metali, bu aşamada büyük bir basınç altında olan kalıbın içinden iter.
Koç ile ısıtılmış kütük arasındaki teması önlemek için, genellikle aralarına malzeme blokları yerleştirilir. Bu uygulama, doğrudan temas olmamasını sağlayarak sürecin verimliliğini artırır. Hem alüminyum kütük hem de ram birleşik bir ileri yönde hareket ettiğinden, bu yöntem "ileri ekstrüzyon" unvanını kazanmıştır.
Dolaylı Alüminyum Ekstrüzyon Tekniği
Geriye doğru ekstrüzyon olarak da adlandırılan dolaylı yöntem, doğrudan muadilinden temelde farklıdır. Bu yaklaşımda, kalıp yerinde sabit kalırken kütük ve kabı hareket eden bileşenlerdir. Prosedürde, kabın uzunluğunu aşan ve koçu sabit tutan bir "mil" kullanılır. Sonuç olarak, alüminyum kütük hareket etmeyen kalıbın içinden itilir.
Dolaylı yöntemin bir avantajı, sürtünmeyi azaltarak üstün ısı düzenlemesine yol açmasıdır. Sonuç olarak, dolaylı ekstrüzyondan elde edilen ürünler genellikle gelişmiş tutarlılık sergiler. Bu, tutarlı kuvvet uygulamasına ve tek tip sıcaklığa atfedilebilir, bu da daha iyi mekanik özellikler ve tane konfigürasyonu ile sonuçlanır.
Alüminyum Ekstrüzyon Sürecine Kapsamlı Bir Bakış
Adım 1: Ekstrüzyon Kalıbının Kurulumu
Dairesel bir kalıp işleyerek başlayın veya önceden var olan bir kalıbı tercih edin. Düzgün metal akışı sağlamak ve kalıbın ömrünü uzatmak için bu kalıbı 450-500°C arasında önceden ısıtmak çok önemlidir. Önceden ısıtıldıktan sonra kalıbı ekstrüzyon presinin içine yerleştirin.
Adım 2: Alüminyum Kütüğün Isıtılması
İlk olarak, sağlam silindirik bir alüminyum alaşım parçası olan kütüğü daha uzun bir malzeme kütüğünden ayırın. Ardından, 400-500°C aralığında bir fırında ısıtın. Bu ısıtma kütüğü sadece esnek hale getirmekle kalmaz, aynı zamanda erimiş değil katı halde kalmasını sağlar.
Adım 3: Kütüğün Preste Konumlandırılması
Isıtma işleminden sonra kütüğü mekanik olarak prese kaydırın. Bunu yapmadan önce, üzerine bir yağlayıcı ve ekstrüzyon koçuna bir ayırıcı madde uygulayarak birbirlerine yapışmamalarını sağlayın.
Adım 4: Kütüğü Pres Konteynerine Yerleştirin
Kütük presin içine girdiğinde, hidrolik bir koç muazzam bir kuvvet uygular - yaklaşık 15.000 ton - esnek kütüğü kabın içine iter ve burada genişleyerek kap alanını kaplar.
Adım 5: Malzemeyi Kalıptan Geçirmek
Kütük kabın içindeyken, sürekli uygulanan basınç nedeniyle kalıba doğru bastırılır. Malzemenin tek çıkışı kalıbın açıklıklarıdır, bu da ortaya çıkarken istenen şekle neden olur.
Adım 6: Soğutma Aşaması - Su Verme
Ekstrüzyon çıkarken, bir çektirme onu tutar ve yönlendirir. Tabla üzerindeki yolculuğu sırasında, "su verme" olarak adlandırılan bir prosedür olan fanlar veya su banyosu ile soğutmaya tabi tutulur.
Adım 7: Ekstrüzyonların Tabla Uzunluğuna Uygun Şekilde Kırpılması
Tablanın tam uzunluğuna ulaşıldığında, sıcak bir testere ekstrüzyonu keser. Söndürme işleminden sonra bile ekstrüzyonun bir miktar ısı tuttuğunu belirtmek gerekir.
Adım 8: Son Soğutma Aşaması
Kesme işleminden sonra, ekstrüzyonları ortam sıcaklığına ulaşana kadar kalacakları bir soğutma alanına kaydırın. Bu soğutma germe için zemin hazırlar.
Adım 9: Germe ve Hizalama
Bu noktada, şekillerde bazı küçük bozulmalar gözlemleyebilirsiniz. Bunları bir sedye kullanarak, her bir profili her iki ucundan tutarak ve düz bir konfigürasyon ve istenen özellikleri elde etmek için gererek giderin.
10. Adım Hassas Uzunluklarda Kesme
Düzeltilmiş, işle sertleştirilmiş ekstrüzyonlarla, artık bunları hassas kesimler için bir testere masasına taşıyabilirsiniz, öncelikle 8-21 ft arasında değişir. Bunu takiben, T5 veya T6 gibi ideal temperlemeyi elde etmek için yaşlandırılmak üzere bir fırına taşınabilirler.
Adım 11: Ek Prosedürlerle Sonlandırma
Ekstrüzyon işlemi sona erdiğinde, profiller belirli özellikleri geliştirmek için ısıl işlemlere tabi tutulabilir. Isıl işlem sonrası, gerekirse, imalat herhangi bir boyutu düzeltebilir. Son olarak, estetiği artırmak ve korozyon direncini güçlendirmek için bir yüzey kaplaması uygulayın.