Aluminum Billet Production: Quality Surface, High Performance
Kenan Metal's high purity aluminum billet production and advanced casting technology offer industry-specific solutions. Discover the details that make a difference for quality production.
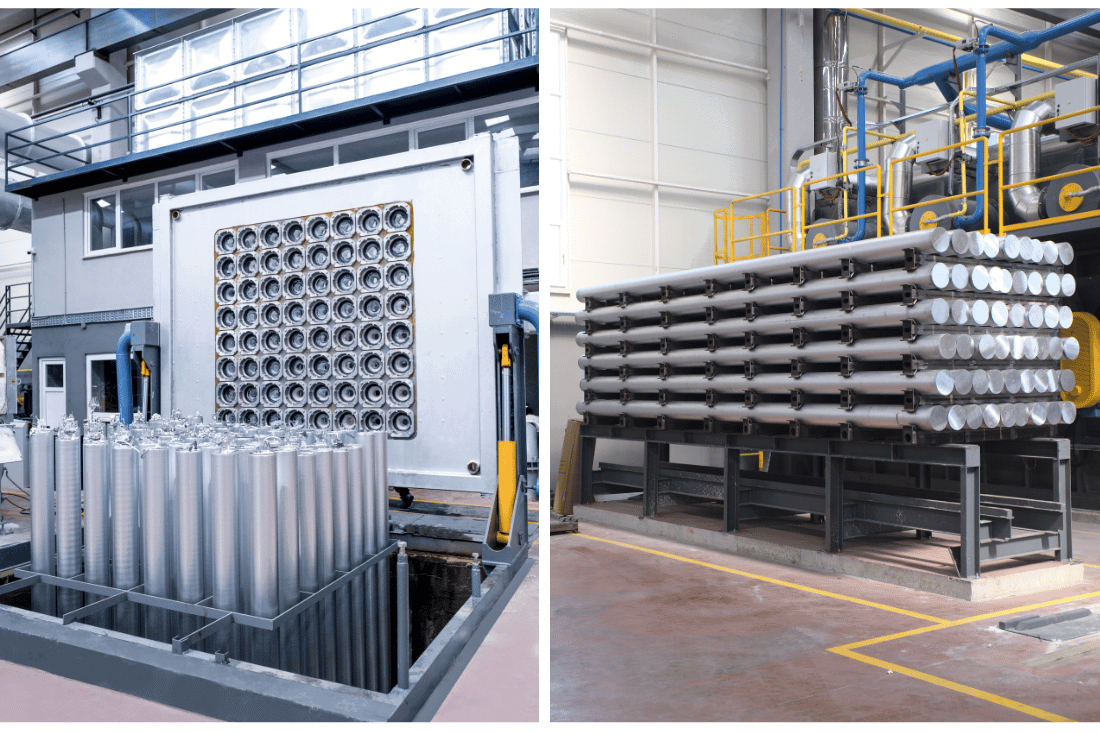
Aluminum billet production is one of the basic building blocks of modern industrial production. The quality of profiles used especially in automotive, construction, defense industry and architectural facade systems directly depends on this production process. As Kenan Metal, we are based on high purity, technical precision and compliance with customer demands in the aluminum billet production process.
Our modern production infrastructure is optimized at every step, from casting technology to mold design. The basis of our production is the preparation of aluminum ingots with ideal alloy ratios, followed by casting techniques that provide a homogeneous structure to form billets in the desired size and properties.
Content Suggestion: High-Quality Aluminum Billet Production by Kenan Metal
Content Suggestion: Aluminum Billet: Indispensable in the Industrial World
What is Aluminum Billet?
Aluminum billet is a semi-finished form used before extrusion. These bars are prepared in specific diameters and lengths and are made suitable for forming by heat treatment. High surface quality, microstructural homogeneity and alloy stability ensure that a billet is an efficient and high quality end product.
Kenan Metal's Power in Billet Manufacturing
1- Advanced Casting Technology
Kenan Metal applies semi-continuous casting technology with high precision in aluminum billet production. This method offers an advanced process infrastructure that enables controlled cooling and solidification of liquid aluminum during casting, maintaining thermal stability and dimensional integrity. Thanks to this method:
- The formation of microcracks and porosity is minimized. The controlled solidification of the metal ensures homogeneity in the internal structure and prevents internal defects that may occur during extrusion.
- Thermomechanical stability is achieved. A consistent crystallization structure is created across the entire cross-section of the material, which improves both mechanical strength and surface quality.
- Linear stability is maintained in long billet production. Despite the increased length of the billet, the risks of warping, cracking and internal stress are minimized.
- Surface quality and circularity tolerances are kept within a narrow band. This extends the life of the extrusion dies and improves the performance of the final product.
2- Alloy Control
In applications requiring high performance, one of the most critical parameters in material selection is the correct alloy design and control. Kenan Metal produces aluminum alloy grades such as EN AW-6063, EN AW-6082, EN AW-6005 in accordance with international norms and multi-purpose and sectoral standards. In this process:
- With spectrometer-supported chemical analysis, the alloy composition of each casting batch is instantly measured and reported.
- High purity primary aluminum and additives (Mg, Si, Mn, Fe, etc.) are added with automatic dosing systems to ensure chemical traceability.
- Each alloy type is optimized according to the application area. For example:
- EN AW-6063: Ideal for high surface quality and decorative anodizing performance in architectural profile systems.
- EN AW-6082: Suitable for automotive and conveyor systems requiring high strength and workability.
- EN AW-6005: It is preferred in the construction and energy sector with its medium-load carrying capacity.
3- Homogenization and Heat Treatment
The billets obtained after casting are heat treated in homogenization furnaces for mechanical and metallurgical stability. Thanks to this critical process:
- Precipitates in the aluminum matrix are dissolved so that the alloying elements are evenly distributed in the microstructure.
- Stress zones in the crystal structure are eliminated, thus preventing profile deformations during extrusion.
- The metallographic structure becomes fine-grained and isotropic, which positively affects the parameters of the product such as ductility, impact strength and surface quality.
- Segregation and band structures that may occur in the internal structure of the billet are minimized, resulting in more consistent extrusion behavior.
Criteria to be Considered in Aluminum Billet Production
The following criteria are critical for the production of a high quality aluminum billet:
- Low gas and particle content
- Homogeneous structure and minimization of internal stress
- Excellent surface quality
- Tailored diameter and length tolerances
- Preservation of alloy purity
All of these criteria are central to the Kenan Metal production process.
Areas of Use and Application Advantages
Kenan Metal aluminum billets are specially developed for use in the following areas:
- Architectural facade systems
- Outdoor shading and air conditioning solutions
- Automotive industry profiles
- Energy transportation systems (e.g. solar panel carriers)
Our ability to manufacture custom sizes and alloy compositions for each project gives our partners maximum design and performance flexibility.
The Difference of Kenan Metal
- High production capacity and modern machinery
- Customer-oriented customized production solutions
- Compliance with international quality standards (ISO 9001, EN 755-9 etc.)
- Expert technical staff and engineering support
Kenan Metal is not only a supplier in aluminum billet production, but also a strategic solution partner that optimizes the production processes of its business partners.
Within the scope of our sustainability policy, we minimize our environmental footprint by using recycled aluminum. At the same time, we reduce carbon emissions in the production process by using energy efficient equipment.
With the assurance of Kenan Metal, each billet is shaped by the principles of quality, precision and sustainability. Whatever your project, if you are looking for a reliable and stable production partner, you are in the right place.